1.The major structures are manufactured
from Meehanite cast iron, stress relieved and combined
with scientific rib reinforcement to ensure deformation-free
operations.
2.Increase width on the column bottom with box-type
structure provides maximum stability especially when
performing high speed cutting.
3.Linear ways on three axes assure high feed rates
and extremely smooth motion.
4.Extra wide span between linear ways greatly increases
machine stability.
5.The structural parts are analyzed and designed
by the advanced Finite Element Analysis. It provides
a detailed analysis for structural stress/strain
conditions, and ensures excellent machine rigidity
and lifetime stability.
6.Linear guide ways:
The machine employs 45mm wide ball-type linear guide
ways. (Optional)
7.Precision ball screw:
Three axes are transmitted by high precision C3 grade
ball screws, preloaded, hardened and ground-assuring
dependable feed accuracy.
8.Choice of 30,000 rpm high speed spindles are designed
for high speed machining requirement.
9.Extra wide column bottom and base ensure simplified
machine structure for space saving.
10.The three axes ball screws are directly coupled
to servos through backlash-free couplings. This ensures
dependable positioning accuracy. High precision class
C3 ball screws are preloaded to eliminate thermal
strain.
The structural parts are analyzed and designed
by the advanced Finite Element Analysis.
The machine employs 45mm wide ball-type linear
guide ways.

Three axes are transmitted by high precision C3
grade ball screws, preloaded, hardened and ground-assuring
dependable feed accuracy.
Choice of various high speed spindle
Belt Drive Spindle
Choice 8000,10000,12000RPM.Spindle taper BT-40
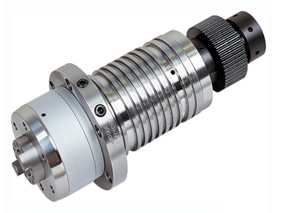
Direct Drive Spindle
Choice 10000,12000,15000RPM. Spindle taper BT-40
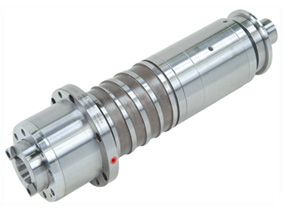
Build in Type Spindle
Choice 24000,30000RPM. Spindle taper HSK-50E

|
Carousel type magazine
The carousel type magazine is standard equipment.
It carries 16 tools for various types of machining
applications.Fixed type tool selection for quick
tool changing that reduces non-cutting time.
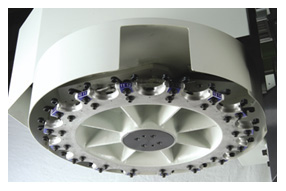 |
Arm type magazine(Optional)
The magazine is driven by a precision cam for rapid
and stable tool change motion. Tool loading capacity
provides 20 or 24 tools to choose from. Bi-directional
random tool selection provides quick tool changing
that reduces non-cutting time.
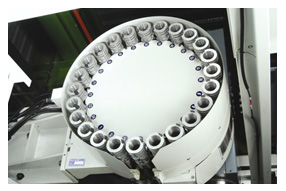
|
Directly coupled servomotors:
The three axes ball screws are directly coupled to
servos through backlash-free couplings. This
ensures dependable positioning accuracy. High
precision class C3 ball screws are preloaded
to eliminate thermal strain.
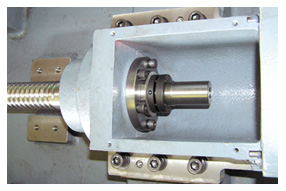 |
Coolant flushing device(Optional):
Three coolant nozzles are provided on both sides
of the table featuring high pressure flushing
to remove chips from the table.
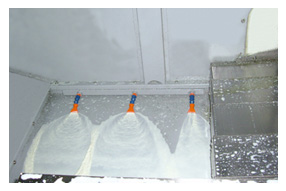
|
4th CNC rotary table(Optional)
The 4th CNC rotary table features high positioning
accuracy and maximum stability during cutting. It
is ideal for various types of workpiece machining.
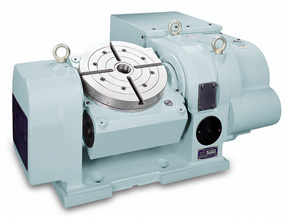 |
Spindle splash ring (Optional):
The spindle splash ring is available only for models
with arm-type magazine. The device not only effectively
removes chips on work piece but also increases
work piece cooling efficiency.
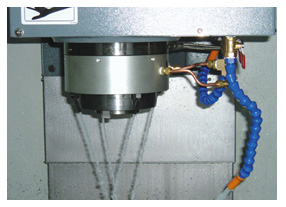 |
Ball bar test:
Through ball bar testing the circularity, geometry
error and backlash can be accurately obtained allowing
the machine to be adjusted to the best possible
accuracy.
 |
Laser inspection:
An advanced laser instrument is employed for inspecting
and compensating linear accuracy and pitch error.
This ensures optimum axis travel accuracy.
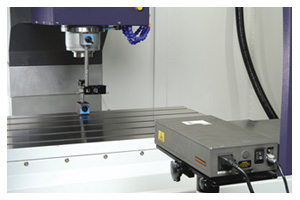 |
Heat exchanger for controller cabinet:
To maintain a constant temperature inside the control
cabinet, the machine is equipped with a heat
exchanger. It provides effective protection for
the controller and electronic components. The
high performance heat exchanger features high
efficiency heat exchange and power saving.
 |
Spindle oil cooler:
It prevents spindle thermal deformation due to oil
temperature variation while ensuring high machining
accuracy, especially at high spindle speeds.
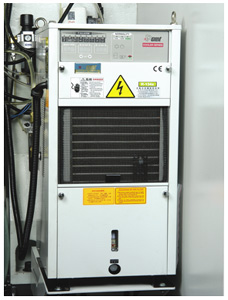
|
Inspection Procedures:
1. Geometric Accuracy Inspection.
2. Spindle Balancing Adjustment.
3. Full running test 24 hours before delivery.
4. Practical work piece machining test.
5.Water tank leakage test.
6. Machine functional test |